Throughout the winter break Motorsport Week will be providing insight into the various machinations of the Formula 1 world. Today we take a look at the logistics of getting everything around, by sea, air and road.
The Formula 1 community is in effect a small army that needs to get from A to B 22 times per year, keeping the show on the road; transporting people is easy, but what about all of the equipment?
By road, sea and air the logistics of Formula 1 are planned down to the hour, if not the minute, with teams having partners for the European rounds, and utilising championship partner DHL for ‘flyaway’ events.
For air freight DHL uses six Boeing 747 cargo planes, each with the capacity to hold 130 tons of equipment, to fly race critical equipment around the world from event to event. DHL also has a seventh plane on standby just in case additional equipment is needed.
The ‘race critical’ equipment classifies as components that are vital for the grand prix to take place, such as pit equipment, computer servers, the broadcast centre, tyres, engines and of course car components. After each race, following mandatory post-race checks by scrutineers, the cars are stripped down and packed away into tailor-made foam-lined containers, with the cargo crates specifically designed to slot into place on the plane like a jigsaw. In the interests of fairness the teams are notified of when their cargo must be present – in the case of UK-based teams this location is East Midlands Airport – while at grands prix car build can only commence once all the cargo crates have been unloaded at the circuit. Formula 1 has had delays in the past but nothing that has significantly impeded the running of a grand prix. In 2010 the eruption of Iceland’s Eyjafjallajökull volcano caused severe disruption to air travel but a three-week gap after the concurrent Chinese GP weekend alleviated any concerns, while weather systems that have the potential to hinder events (such as Typhoon Hagibis in 2019) have not affected Sunday or Monday to a damaging extent, while possible visa and customs setbacks are usually cleared. The toughest events logistically are typically the back-to-back events that involve long distances, tough customs requirements or a disadvantageous time zone change. That would currently be Singapore to Russia. Moving east to west at least ensures the paddock ‘gains’ five hours, but the late start in Singapore means everyone is already six hours behind the usual ‘European’ schedule.
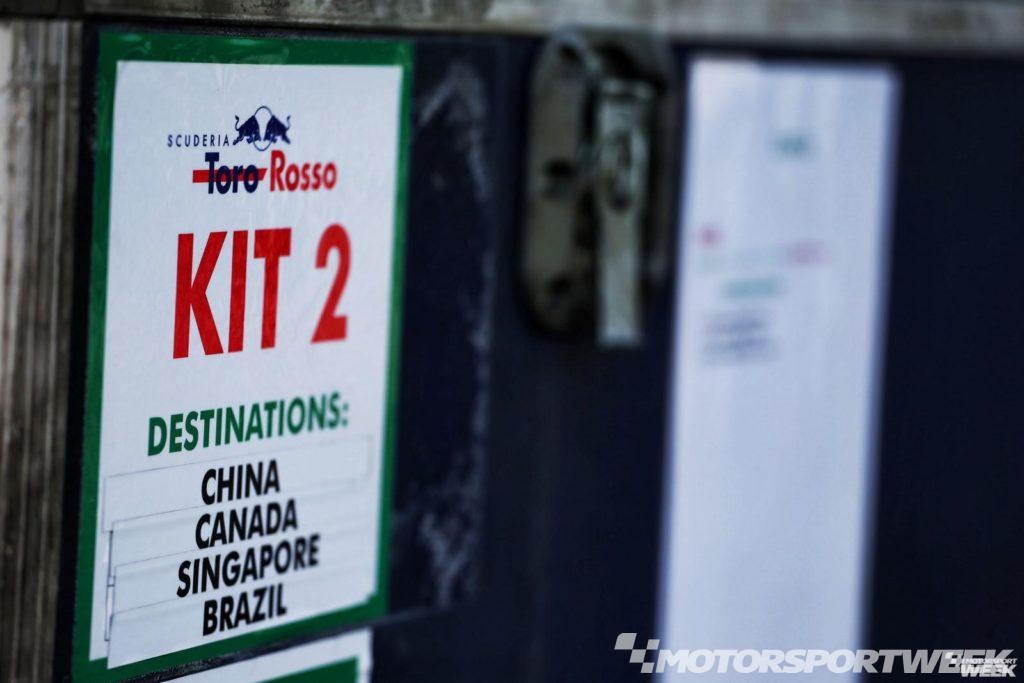
What doesn’t need to go by air can go by sea.
Sea freight takes longer but is cheaper and environmentally friendlier. Each team has five sets of the same non-critical equipment that is often locked away in a container on a vessel somewhere in the ocean. This can include items relating to hospitality – such as cutlery, tables, chairs and even long-lasting dried foods – equipment for marketing purposes, and other associated sundries, for example barriers and garage panels. One batch will be shipped off to Australia in mid-January, and after the season opener its next event will be Canada, and then Brazil. Another set will work their way from Bahrain to Russia and then to Abu Dhabi. In a 22-race season some of the equipment may only ‘do’ two or three events such is the need for forward-thinking and efficient transportation. It is cheaper and easier to have five lots of the same equipment than get the same one to each event. In some instances it is more cost-effective to buy the equipment for just one event (such as a printer) and then discard it afterwards, rather than transport it around the world. Mistakes can happen. One marque’s sea freight container was accidentally left in Felixstowe, UK, rather than put on the ship for the eight-week voyage to Mexico in 2018. DHL nobly paid the $56/kilo air freight fee for the necessary equipment to get to the race in the two-week gap that was remaining, once the error was realised.
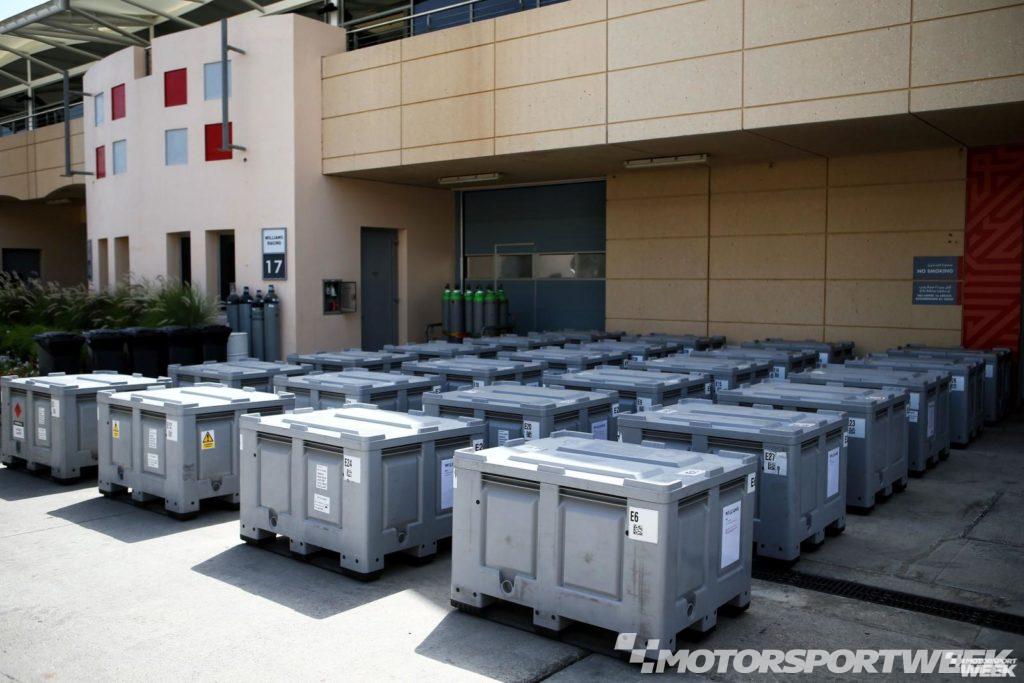
For the European events Formula 1 teams typically use their own logistics partner and methods to transport equipment from A to B, with a legion of around 300 articulated lorries used to get the championship around. Each team has around 25 trucks, plus those from Honda, Pirelli and the FIA. For an F1 team around two-thirds of the lorries are used to transport the motorhome, with the remaining third carrying the race equipment. They are joined by the Formula 2, Formula 3 and Porsche Supercup teams and organisers at most of the European events. Teams use vans for faster transportation on some equipment both for convenience and because of the tight European Union regulations on driving duration restrictions for lorry drivers, which can require extended rest periods or the use of multiple drivers. Accidents can happen, such as the one which affected Renault en route between Germany and Hungary last year, but fortunately the equipment went undamaged while the driver was unharmed. The most challenging sequence for Formula 1 came in 2018, with a triple header across France, Austria and Britain, requiring long driving distances, some rapid turnaround times, and additional hands. Mercedes doubled its usual 30-person crew in order to ensure its motorhome was ready, reducing the usual three-day build and 24-hour deconstruction, and putting the metal framework (last section to be removed, first part needed for construction) in a Sprinter van for faster transportation. A couple of teams used a different motorhome for the middle event in Austria and took their usual unit straight from France to Britain. Every minute counts for the near day-long journey between some European events.
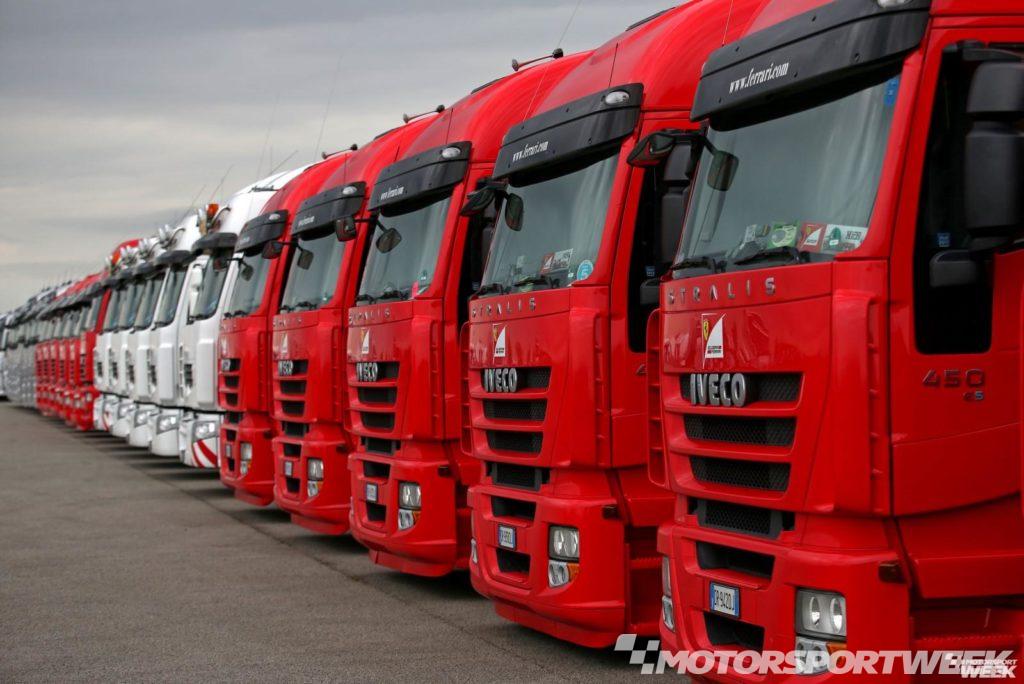
So the next time you watch a grand prix on a Sunday afternoon just think of all the cars, engines, tyres, fuel, hospitality units, broadcast equipment, food, pit walls, garage awnings, barriers, computers, sensors, pit lane equipment, wires and cables, spanners, pots and pans that need to be taken too. Everything – including the kitchen sink.